Plasma cutting is a vital technology used in industries ranging from automotive to construction, providing a fast, efficient method for cutting metal with high precision. As technology advances, so do the systems that drive this process. Among the key elements that ensure optimal plasma cutting performance are torch height control, the THC plasma cutter, Mach3 plasma setup, and specialized software like PlasmaDiv. These components work in tandem to ensure that the plasma cutter operates at peak efficiency, delivering smooth, precise cuts on a variety of materials. In this article, we will explore each of these essential technologies, focusing on how they contribute to the overall plasma cutting process, and highlight their individual significance in the broader picture of industrial fabrication. Whether you are new to plasma cutting or seeking ways to improve your system’s performance, understanding these technologies will be critical to achieving the best results possible. Let’s dive into the key components of plasma cutting systems.
Torch Height Control – Ensuring Precision in Plasma Cutting
Torch height control (THC) is one of the most critical aspects of a plasma cutting system. It directly influences the quality of the cut, the efficiency of the process, and the lifespan of both the consumables and the machine itself. The primary function of torch height control is to maintain a consistent distance between the plasma torch and the workpiece during cutting. This distance is crucial because it ensures optimal arc stability and heat distribution, leading to smoother cuts and improved material handling.
Without proper torch height control, the plasma arc can become unstable, leading to several issues. If the torch is too close to the material, it may cause the plasma arc to “short out,” which could result in poor cut quality, increased wear on the nozzle, and excessive spatter. On the other hand, if the torch is too far from the material, the arc will lose power, resulting in an uneven cut and potential inaccuracies. Therefore, maintaining an optimal height is essential for achieving high-quality results.
There are two primary types of torch height control systems: manual and automatic. Manual systems require the operator to adjust the torch height by hand, which can be time-consuming and prone to human error. Automatic torch height control, however, is the preferred method for modern plasma cutters. This system continuously adjusts the height of the torch in real-time as it moves across the workpiece, responding to changes in the material’s surface. Automatic THC uses sensors to measure the distance from the torch to the workpiece and adjusts the height accordingly, ensuring a consistent gap is maintained throughout the cut.
The benefits of automatic torch height control are numerous. One of the most significant advantages is that it allows for faster cutting speeds and better consistency. By ensuring that the torch height remains constant, the system prevents issues such as arc instability and inconsistent cuts, leading to higher productivity and less material waste. Additionally, automatic THC systems can adjust to changes in material thickness, ensuring that the cutting process remains precise regardless of the workpiece’s profile.
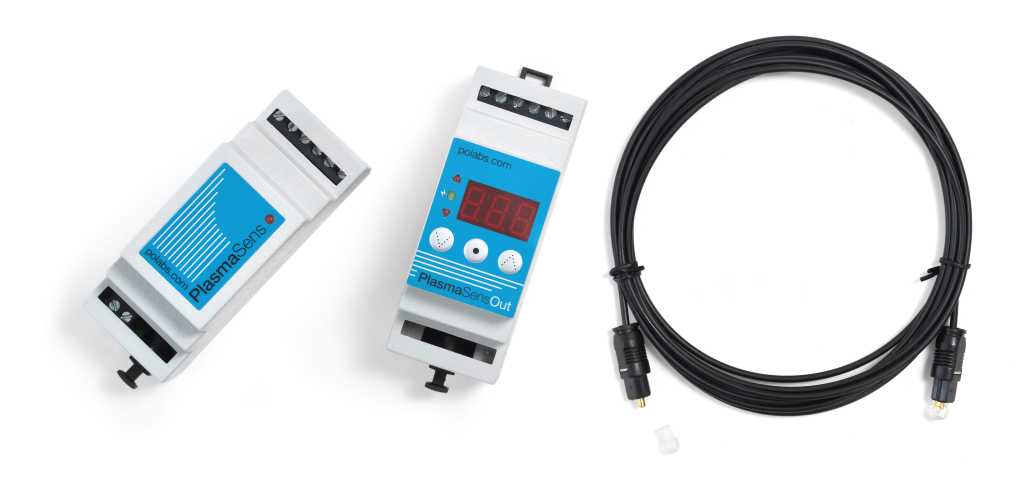
Another important aspect of torch height control is its effect on consumable lifespan. Plasma cutting consumables, including nozzles and electrodes, are subjected to intense wear during the cutting process. When the torch height is not maintained properly, these parts can wear out more quickly, leading to higher maintenance costs and more frequent replacements. Automatic THC reduces the strain on consumables by maintaining a steady torch height, ultimately extending their lifespan and reducing the need for costly replacements.
Integrating torch height control with other components of the plasma cutting system, such as the THC plasma cutter, can further enhance the cutting process. The THC plasma cutter is designed to work in harmony with the torch height control system, making real-time adjustments to the torch height for optimal results. This synergy between the two technologies ensures that the cutting process remains stable, even when faced with challenging materials or irregular surfaces.
In summary, torch height control is a cornerstone of modern plasma cutting systems. By ensuring that the torch maintains a consistent distance from the material, it plays a crucial role in achieving high-quality cuts, maximizing the efficiency of the system, and extending the lifespan of consumables. Whether using a manual or automatic system, maintaining proper torch height is essential for ensuring that the plasma cutter operates at its best.
THC Plasma Cutter – The Heart of Height Control and Cutting Efficiency
A THC plasma cutter, or Torch Height Control plasma cutter, is an essential component of modern plasma cutting systems, ensuring that the cutting process remains accurate and efficient. This system works by automatically adjusting the height of the plasma torch during the cutting operation, which is critical for maintaining a consistent and optimal distance between the torch and the workpiece. Without a properly functioning THC plasma cutter, the overall quality of the cut can suffer, leading to issues such as uneven cuts, excessive material waste, and premature wear on the consumables.
The primary role of a THC plasma cutter is to regulate the height of the torch above the surface of the material being cut. The plasma arc is highly sensitive to changes in distance, and even small variations can result in poor cut quality or inefficiency. By automatically adjusting the height of the torch, the THC plasma cutter ensures that the plasma arc remains stable, producing clean, precise cuts without the fluctuations that might otherwise occur. This results in a much higher level of cutting precision and overall performance compared to manual height adjustments.
One of the most significant advantages of a THC plasma cutter is its ability to respond in real-time to changes in the workpiece’s surface. Materials often have uneven surfaces or varying thicknesses, and these variations can cause the plasma arc to become unstable. The THC plasma cutter addresses this by using sensors to measure the distance between the torch and the material, continuously adjusting the height as needed. This adaptability ensures that the plasma arc remains optimal throughout the entire cut, reducing the likelihood of issues such as poor cut quality, excessive slag, or inconsistent edge finishes.
In addition to maintaining optimal cutting conditions, the THC plasma cutter plays a crucial role in protecting the plasma torch and consumables. When the torch is too close to the material, excessive heat can cause the nozzle and electrode to wear out faster, leading to increased maintenance costs. If the torch is too far away, the plasma arc may become unstable, resulting in erratic cuts and more frequent nozzle replacements. By ensuring that the torch height is always in the ideal range, a THC plasma cutter helps extend the lifespan of consumables, leading to reduced downtime and lower operational costs.
Another notable benefit of using a THC plasma cutter is its impact on cutting speed. With precise height adjustments, the system allows for faster cutting speeds without sacrificing cut quality. This is particularly valuable in high-volume production environments, where time efficiency is a key factor in profitability. The THC plasma cutter minimizes the need for manual adjustments, freeing up the operator to focus on other aspects of the job, thus increasing overall productivity.
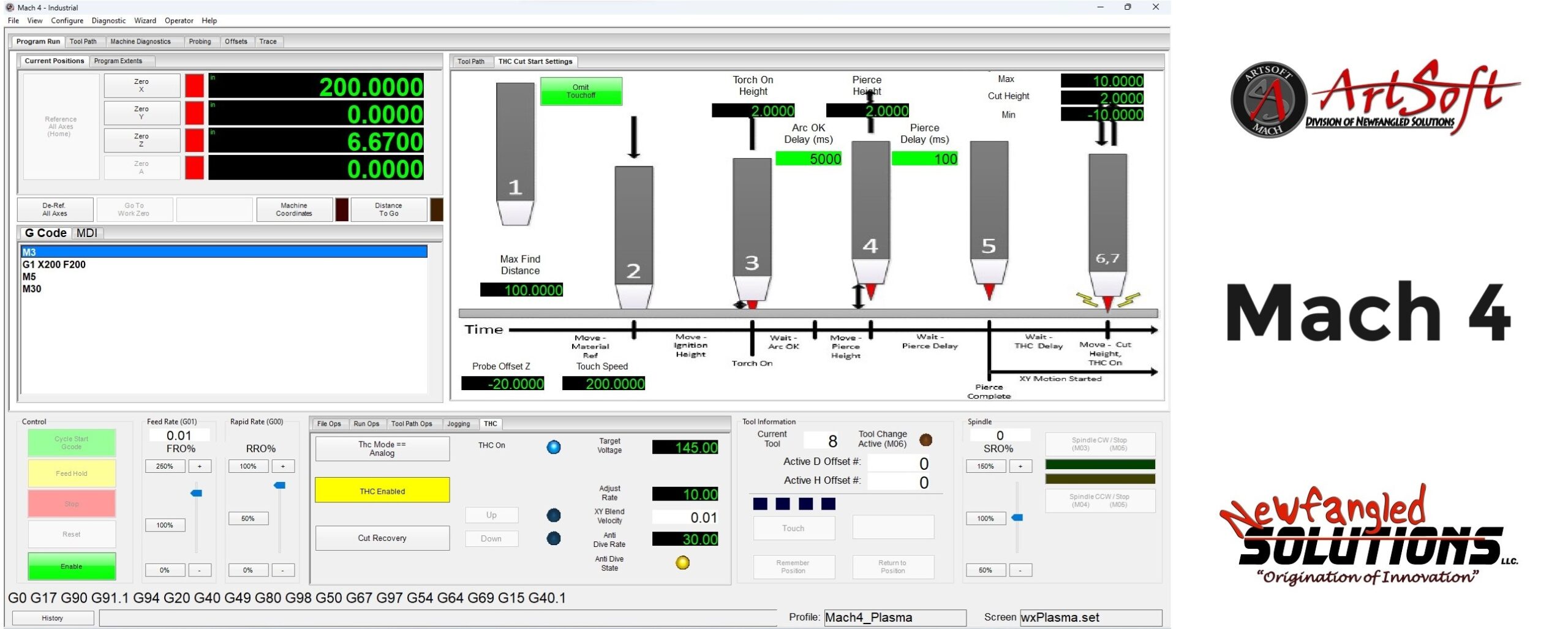
The integration of a THC plasma cutter with advanced software and CNC controls further enhances its capabilities. By combining the precision of the THC plasma cutter with the power of computer numerical control (CNC) systems, operators can achieve highly complex cuts with minimal effort. The system can be programmed to cut intricate shapes and patterns with ease, all while maintaining consistent torch height for optimal cutting performance.
In modern plasma cutting systems, the THC plasma cutter works hand-in-hand with other technologies, such as the torch height control system and Mach3 plasma setup, to create a seamless cutting experience. When these systems are integrated, the THC plasma cutter ensures that the cutting process remains as efficient, precise, and reliable as possible.
In conclusion, a THC plasma cutter is indispensable for modern plasma cutting systems. By automating the process of adjusting the torch height, it ensures consistent, high-quality cuts and protects the longevity of consumables. Its ability to respond to changes in material surface and thickness makes it an essential tool for industries that demand precision, speed, and reliability in their cutting processes. Whether in a production setting or for more intricate, detailed work, the THC plasma cutter is a key player in achieving the best results in plasma cutting operations.
Mach3 Plasma Setup – Enhancing CNC Plasma Cutting Precision
When it comes to modern plasma cutting, precision and control are paramount. A Mach3 plasma setup plays a crucial role in ensuring that the cutting process is not only efficient but also highly accurate. Mach3 is a popular and widely used CNC (Computer Numerical Control) software that allows users to control plasma cutting machines with great precision. Whether you’re working in a small shop or a large manufacturing facility, setting up and configuring Mach3 for plasma cutting is a key step in maximizing the performance of your system.
Mach3 works by interpreting G-code instructions and converting them into movements for the CNC plasma cutter. These instructions control the movement of the torch, the speed of the cut, and other key parameters of the plasma cutting process. One of the primary reasons why Mach3 is so widely used in plasma cutting setups is its flexibility and ease of use. It offers an intuitive interface that allows operators to easily configure and modify settings for their plasma cutting machines. Additionally, Mach3 supports a wide range of hardware, making it compatible with many different types of CNC plasma cutters and controllers.
A key aspect of setting up Mach3 for plasma cutting is ensuring that the software is properly calibrated with the hardware components of the system. This includes configuring the torch height control (THC), which is vital for maintaining optimal cutting conditions throughout the process. Mach3 allows users to adjust settings for the THC plasma cutter, ensuring that the torch height remains consistent regardless of variations in the workpiece’s surface. By properly setting up Mach3, the system can automatically make real-time adjustments to the torch height, reducing the risk of errors and improving the overall cut quality.
Mach3 also offers advanced control over other important aspects of plasma cutting, such as feed rates, dwell times, and pierce times. These parameters are essential for achieving the best results when cutting different materials and thicknesses. For instance, when cutting thicker materials, slower feed rates and longer pierce times may be required to ensure that the plasma arc fully penetrates the material. Mach3 allows users to fine-tune these parameters to suit specific job requirements, ensuring that each cut is made with the right settings for optimal results.
Another important feature of a Mach3 plasma setup is the ability to create and manage toolpaths. Toolpaths define the precise movements the plasma cutter will follow during the cutting process. With Mach3, users can import G-code generated from CAD (Computer-Aided Design) or CAM (Computer-Aided Manufacturing) software, which contains the instructions for cutting intricate shapes and patterns. Mach3 then translates this code into specific movements that guide the plasma torch along the desired path. This ability to create and modify toolpaths gives operators the flexibility to work on complex projects, such as custom fabrication or intricate designs, with a high degree of accuracy.
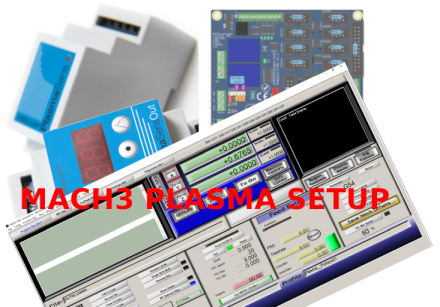
One of the most valuable aspects of the Mach3 plasma setup is its compatibility with various plugins and additional modules. For instance, you can integrate the system with advanced height control features, including those that rely on automatic THC adjustments. Additionally, the Mach3 software can be configured to work seamlessly with the THC plasma cutter, enhancing its real-time responsiveness to changes in the workpiece surface. This integration ensures that the torch maintains an optimal height at all times, further enhancing the precision of the cuts and extending the life of consumables.
Furthermore, Mach3’s versatility extends beyond simple plasma cutting. With its powerful control system, Mach3 can be used for a variety of cutting and milling applications, making it a valuable tool for shops that perform multiple types of operations. Its adaptability also makes it a go-to choice for operators who need to make adjustments or tweak settings in the middle of a job, allowing them to quickly optimize the system’s performance.
In summary, the Mach3 plasma setup is a critical component in modern CNC plasma cutting operations. By offering a flexible and intuitive interface, Mach3 enables operators to configure and control every aspect of the cutting process, from torch height control to toolpath creation. Its ability to integrate with other technologies, such as THC plasma cutters, ensures a seamless and highly accurate cutting experience. Whether you are working with simple designs or complex, custom projects, the Mach3 plasma setup is a powerful tool that can help you achieve the highest levels of precision and efficiency in your plasma cutting operations.
PlasmaDiv – Streamlining Plasma Cutting Operations with Advanced Software
In the world of plasma cutting, advanced software solutions are essential for optimizing the cutting process and improving operational efficiency. PlasmaDiv is one such software tool that is specifically designed to enhance the capabilities of plasma cutting machines, offering features that streamline workflow, improve cut quality, and increase overall productivity. By providing advanced control over the plasma cutter’s operation, PlasmaDiv ensures that businesses can achieve better results with fewer errors, reduced downtime, and more consistent outputs.
PlasmaDiv is particularly notable for its ability to integrate seamlessly with CNC-controlled plasma cutting systems, such as those set up with Mach3. As a software solution, PlasmaDiv offers a range of features that allow users to manage, modify, and optimize their plasma cutting operations. These include enhanced torch height control, the ability to create and adjust toolpaths, and advanced settings for optimizing cut quality. PlasmaDiv acts as a bridge between the plasma cutter hardware and the operator, enabling real-time adjustments and providing the tools necessary for improving the cutting process.
One of the core features of PlasmaDiv is its advanced control over torch height adjustment. While most plasma cutters rely on basic height control, PlasmaDiv adds an extra layer of precision by offering a more sophisticated control interface. The software continuously monitors the torch’s position and automatically adjusts the height as the material surface changes. This dynamic control allows for more precise cuts, particularly on materials with varying thickness or uneven surfaces. By working in tandem with the THC plasma cutter, PlasmaDiv ensures that the torch remains at the optimal distance from the material, which is crucial for achieving clean, smooth cuts.
Another benefit of using PlasmaDiv in plasma cutting operations is its ability to optimize cutting speeds and feed rates. The software can be used to fine-tune these parameters based on the material being cut, the desired cut quality, and the capabilities of the machine. For example, PlasmaDiv allows operators to adjust settings for different types of metal, ensuring that the plasma cutter operates at the ideal cutting speed for each material. This flexibility helps reduce material waste and improve cutting efficiency, particularly in high-volume production settings.
PlasmaDiv also integrates advanced nesting capabilities, a feature that is especially beneficial in environments where material usage must be optimized. The nesting function automatically arranges multiple parts or designs on a single sheet of material to minimize waste. This is particularly useful for manufacturers that need to cut multiple pieces from a large sheet of metal, as it maximizes material utilization and reduces overall costs. PlasmaDiv’s nesting software can quickly generate the most efficient layout, saving time and reducing the need for manual intervention.
Furthermore, PlasmaDiv offers enhanced diagnostic tools that help operators monitor the health of their plasma cutting system. These tools provide real-time feedback on various aspects of the cutting process, including the condition of consumables, torch height settings, and cutting speed. With this data, operators can make adjustments before problems arise, preventing downtime and costly repairs. The diagnostic capabilities of PlasmaDiv can also be used to analyze cutting results, identify areas for improvement, and optimize future cuts.
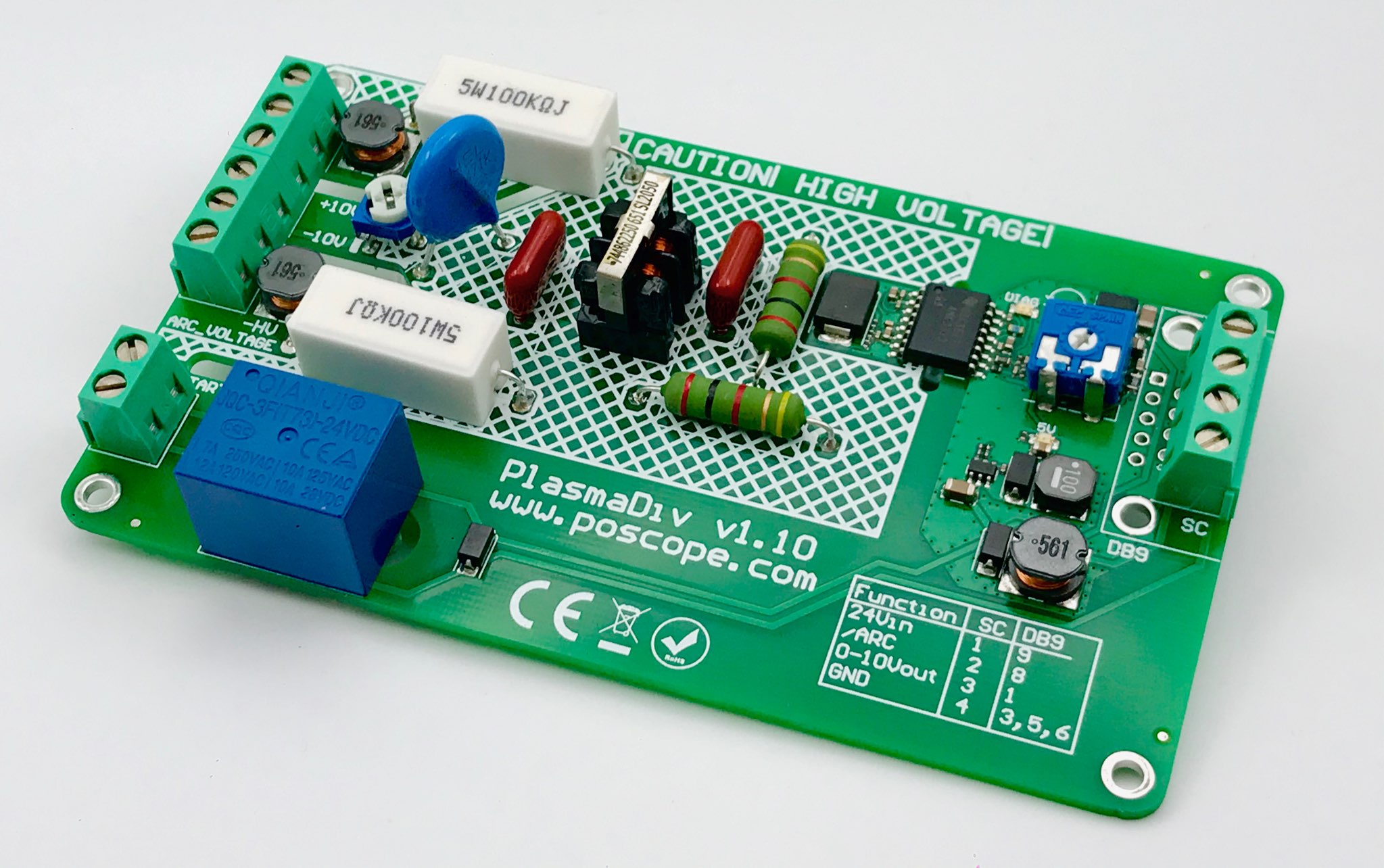
The software’s user-friendly interface makes it accessible even for operators who may not have extensive experience with plasma cutting systems. PlasmaDiv’s intuitive design allows users to quickly learn how to navigate its features, adjust settings, and monitor the cutting process. Additionally, the software is compatible with a wide range of plasma cutting machines, making it a versatile tool for many different types of operations. Whether in a large manufacturing facility or a smaller custom fabrication shop, PlasmaDiv offers the tools needed to streamline plasma cutting operations and ensure consistently high-quality results.
Incorporating PlasmaDiv into a plasma cutting system can also lead to significant reductions in operational costs. By improving cutting efficiency, reducing material waste, and extending the lifespan of consumables, businesses can lower the overall cost of their cutting operations. PlasmaDiv’s integration with other technologies, such as Mach3 plasma setups and THC plasma cutters, helps create a fully optimized system that maximizes productivity while minimizing waste and downtime.
In conclusion, PlasmaDiv is a powerful software solution that enhances the performance of plasma cutting systems by providing advanced control, real-time monitoring, and optimization features. Its ability to fine-tune torch height control, adjust cutting parameters, and optimize material usage makes it an invaluable tool for improving both the quality and efficiency of the cutting process. By integrating PlasmaDiv with technologies like THC plasma cutters and Mach3 plasma setups, plasma cutting operations can be streamlined, leading to faster production times, lower operational costs, and more precise, consistent cuts. Whether used in a large-scale manufacturing environment or a smaller shop, PlasmaDiv is a vital tool for businesses looking to get the most out of their plasma cutting systems.
Conclusion
In the world of plasma cutting, achieving precision, efficiency, and quality requires the seamless integration of various advanced technologies. From torch height control (THC) to specialized software like PlasmaDiv, each component plays a pivotal role in optimizing the plasma cutting process. These systems not only ensure high-quality cuts but also increase productivity, reduce operational costs, and extend the lifespan of consumables, making them indispensable in modern manufacturing and fabrication.
Torch height control, particularly when paired with THC plasma cutters, ensures that the torch remains at an optimal distance from the material, delivering smooth, precise cuts while preventing damage to the nozzle and electrodes. The automatic adjustment of the torch height, facilitated by advanced THC systems, is vital in maintaining arc stability and maximizing efficiency, even when cutting materials of varying thicknesses or uneven surfaces. This real-time responsiveness leads to significant improvements in cut quality and reduces the need for constant manual adjustments, making the process faster and more reliable.
Moreover, the integration of a Mach3 plasma setup adds another layer of precision and versatility, allowing operators to control every aspect of the cutting process. By fine-tuning parameters such as feed rates, pierce times, and toolpaths, Mach3 ensures that plasma cutting operations are executed with the highest level of accuracy. The software’s flexibility enables complex cuts and intricate designs, all while optimizing the torch height and cutting parameters for the best possible results.
Finally, PlasmaDiv, as a cutting-edge software tool, further enhances plasma cutting systems by providing advanced control over torch height, cutting speeds, and material nesting. The software’s ability to fine-tune settings for different materials and cutting scenarios helps improve both productivity and cut quality. By offering real-time diagnostics and feedback, PlasmaDiv allows operators to optimize their systems continuously, reducing downtime and minimizing material waste.
Ultimately, the combination of these technologies—torch height control, THC plasma cutters, Mach3 plasma setups, and PlasmaDiv—creates a highly efficient and precise plasma cutting system that can handle a wide range of cutting tasks with minimal error. Whether you’re working in a high-volume industrial setting or a custom fabrication shop, leveraging these technologies ensures that your plasma cutting system operates at its peak, delivering consistent results, reducing operational costs, and increasing overall productivity. As the industry continues to evolve, these advancements will remain integral to achieving the best possible outcomes in plasma cutting applications.