In the ever-evolving world of engineering and automation, precision and efficiency are paramount. From the intricate movements of a CNC machine to the seamless operation of a model railway, the integration of advanced technologies has transformed how we approach complex tasks. At the heart of this transformation lies the CNC controller, a critical component that ensures the accuracy and reliability of computer-controlled machinery. But the story doesn’t end there. Innovations like the PoKeys57U, a versatile input/output device, have expanded the possibilities for automation, while model railway automation has become a fascinating example of how these technologies can be applied on a smaller scale. Additionally, slip ring testing plays a crucial role in ensuring the durability and performance of rotating systems, further highlighting the interconnectedness of modern engineering solutions. In this article, we will explore these four key topics—CNC controllers, PoKeys57U, model railway automation, and slip ring testing—and examine how they collectively contribute to the advancement of precision engineering and automation.
The CNC Controller – The Brain of Precision Machining
At the core of modern manufacturing and precision engineering lies the CNC controller, a sophisticated device that orchestrates the movements of computer numerical control (CNC) machines. Whether it’s milling, cutting, drilling, or engraving, the CNC controller is the brain that translates digital designs into physical reality with unparalleled accuracy. This chapter delves into the importance of CNC controllers, their functionality, and their impact on industries ranging from aerospace to automotive manufacturing.
A CNC controller is essentially a computer system that interprets design files, often in the form of G-code, and converts them into precise mechanical movements. These controllers manage the motion of motors, spindles, and other components, ensuring that each cut or movement is executed with micron-level precision. For example, in the production of complex aerospace components, where even the slightest deviation can lead to catastrophic failures, the CNC controller’s ability to maintain accuracy is indispensable.
One of the key features of a CNC controller is its ability to handle multiple axes simultaneously. Modern CNC machines often operate with three to five axes, allowing for the creation of intricate geometries that would be impossible to achieve manually. The CNC controller coordinates these axes, ensuring smooth and synchronized movements. This capability is particularly valuable in industries like medical device manufacturing, where components often require complex shapes and tight tolerances.
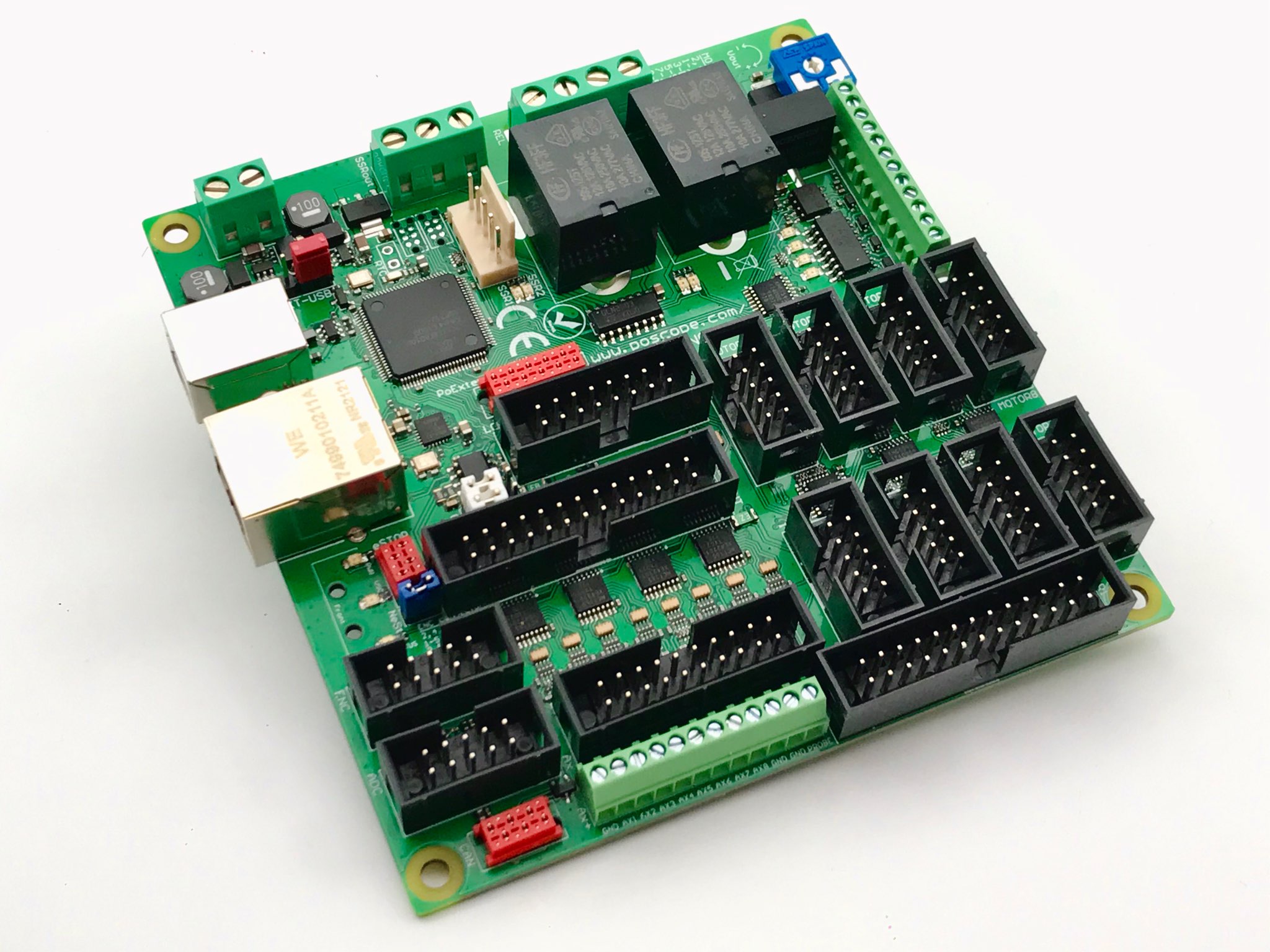
Another critical aspect of CNC controllers is their adaptability. With advancements in software and hardware, modern CNC controllers can be programmed to perform a wide range of tasks. For instance, they can switch between different tools automatically, adjust cutting speeds in real-time, and even detect and correct errors during operation. This flexibility makes CNC controllers a cornerstone of automated manufacturing systems, where efficiency and precision are paramount.
The integration of CNC controllers with other technologies has further expanded their capabilities. For example, the PoKeys57U, a versatile input/output device, can be used alongside CNC controllers to enhance automation. By connecting sensors, switches, and other peripherals, the PoKeys57U enables more sophisticated control and monitoring of CNC machines. This synergy between CNC controllers and devices like the PoKeys57U exemplifies the interconnected nature of modern engineering solutions.
In addition to their industrial applications, CNC controllers have also found a place in hobbyist and educational settings. Enthusiasts use CNC controllers to build custom machines for woodworking, metalworking, and even 3D printing. These applications demonstrate the versatility and accessibility of CNC technology, making it a valuable tool for both professionals and amateurs alike.
Despite their many advantages, CNC controllers are not without challenges. High-end CNC controllers can be expensive, and their complexity often requires specialized knowledge to operate and maintain. However, as technology continues to evolve, these barriers are gradually being lowered, making CNC controllers more accessible to a broader audience.
In conclusion, the CNC controller is a foundational technology that drives precision and automation in modern manufacturing. Its ability to translate digital designs into physical objects with unmatched accuracy has revolutionized industries and opened up new possibilities for innovation. As we explore the other topics in this article—such as the PoKeys57U, model railway automation, and slip ring testing—we will see how the principles of precision and automation embodied by CNC controllers extend into other areas of engineering and technology.
PoKeys57U – The Versatile Enabler of Automation
While the CNC controller serves as the brain of precision machining, devices like the PoKeys57U act as the nervous system, connecting and controlling various components in automated systems. The PoKeys57U is a multifunctional input/output (I/O) device designed to simplify and enhance automation projects. This chapter explores the capabilities of the PoKeys57U, its applications, and how it complements technologies like CNC controllers to create smarter, more efficient systems.
The PoKeys57U is a compact USB device that provides a wide range of I/O options, including digital inputs and outputs, analog inputs, and even support for encoders and stepper motors. Its versatility makes it an ideal solution for hobbyists, engineers, and educators looking to automate processes or create custom control systems. For example, in a CNC machine setup, the PoKeys57U can be used to connect limit switches, emergency stop buttons, and other peripherals, enhancing the machine’s functionality and safety.
One of the standout features of the PoKeys57U is its ease of use. Unlike traditional I/O devices that require complex programming, the PoKeys57U comes with user-friendly software that allows users to configure its functions with just a few clicks. This accessibility has made it a popular choice for model railway automation, where enthusiasts use it to control trains, switches, and signals. By integrating the PoKeys57U into their layouts, hobbyists can create highly detailed and automated railway systems that mimic real-world operations.
In industrial settings, the PoKeys57U is often used to bridge the gap between different components of an automated system. For instance, it can interface with sensors, actuators, and even CNC controllers to create a seamless workflow. This interoperability is particularly valuable in custom automation projects, where off-the-shelf solutions may not meet specific requirements. By leveraging the PoKeys57U’s flexibility, engineers can design tailored systems that optimize efficiency and performance.
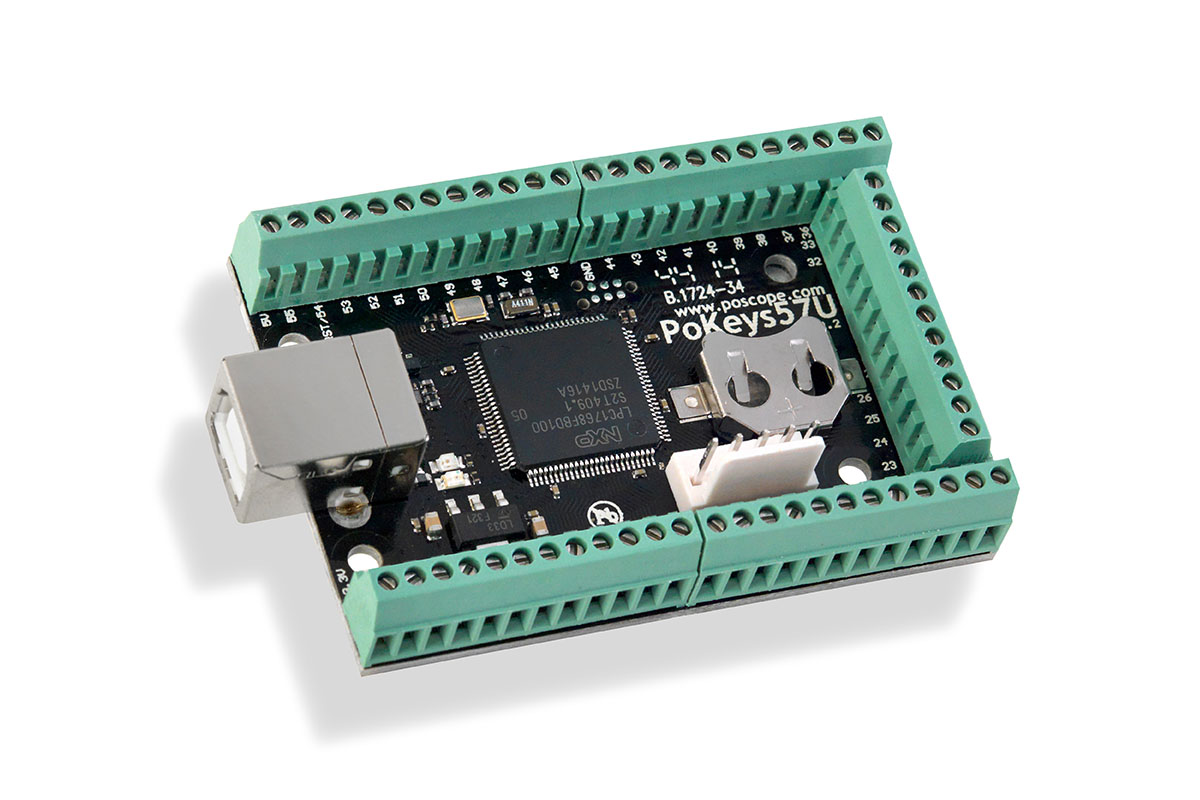
Another notable application of the PoKeys57U is in educational environments. Its affordability and ease of use make it an excellent tool for teaching students about automation and control systems. By working with the PoKeys57U, students can gain hands-on experience in programming, electronics, and system integration, skills that are increasingly in demand in today’s technology-driven world.
The PoKeys57U also plays a role in testing and diagnostics. For example, in slip ring testing, the device can be used to monitor electrical signals and ensure the reliability of rotating connections. This application highlights the PoKeys57U’s ability to adapt to a wide range of tasks, from simple hobby projects to complex industrial processes.
Despite its many advantages, the PoKeys57U is not without limitations. Its USB connection, while convenient, may not be suitable for high-speed or long-distance applications. Additionally, its compact size means that it has a limited number of I/O ports, which may require additional devices for larger projects. However, for many users, the PoKeys57U’s benefits far outweigh these drawbacks.
In conclusion, the PoKeys57U is a powerful and versatile tool that has democratized automation. Its ability to connect and control various components makes it an invaluable asset in projects ranging from model railways to industrial automation. By working in tandem with technologies like CNC controllers, the PoKeys57U exemplifies the collaborative nature of modern engineering solutions. As we move on to explore model railway automation and slip ring testing, we will see how the principles of connectivity and control embodied by the PoKeys57U continue to drive innovation in diverse fields.
Model Railway Automation – A Microcosm of Precision Engineering
Model railways have long been a beloved hobby for enthusiasts who enjoy recreating the intricate details of real-world train systems. However, in recent years, model railway automation has taken this pastime to a whole new level, transforming static layouts into dynamic, lifelike systems. This chapter explores how technologies like CNC controllers and the PoKeys57U are being used to automate model railways, creating a fascinating microcosm of precision engineering.
At the heart of model railway automation is the desire to replicate the complexity and realism of actual train operations. This involves controlling multiple trains, switches, signals, and even scenery elements like lighting and sound. Achieving this level of automation requires precise coordination, much like the tasks performed by a CNC controller in a manufacturing setting. In fact, some advanced model railway setups use CNC controllers to manage the movement of trains and other components with exceptional accuracy.
One of the key challenges in model railway automation is ensuring smooth and reliable operation. Trains must accelerate and decelerate realistically, switches must change positions seamlessly, and signals must respond to train movements in real-time. This is where devices like the PoKeys57U come into play. By connecting sensors, motors, and other peripherals, the PoKeys57U enables hobbyists to create sophisticated control systems that mimic the behavior of real railways. For example, a PoKeys57U can be programmed to detect the position of a train using infrared sensors and automatically adjust signals and switches accordingly.
Another aspect of model railway automation is the creation of intricate scenery and special effects. CNC controllers are often used to fabricate detailed landscape elements, such as bridges, tunnels, and buildings, with precision that would be difficult to achieve by hand. Additionally, the PoKeys57U can control lighting and sound effects, adding an extra layer of realism to the layout. For instance, streetlights can turn on as a train passes through a town, or the sound of a steam engine can be synchronized with its movement.
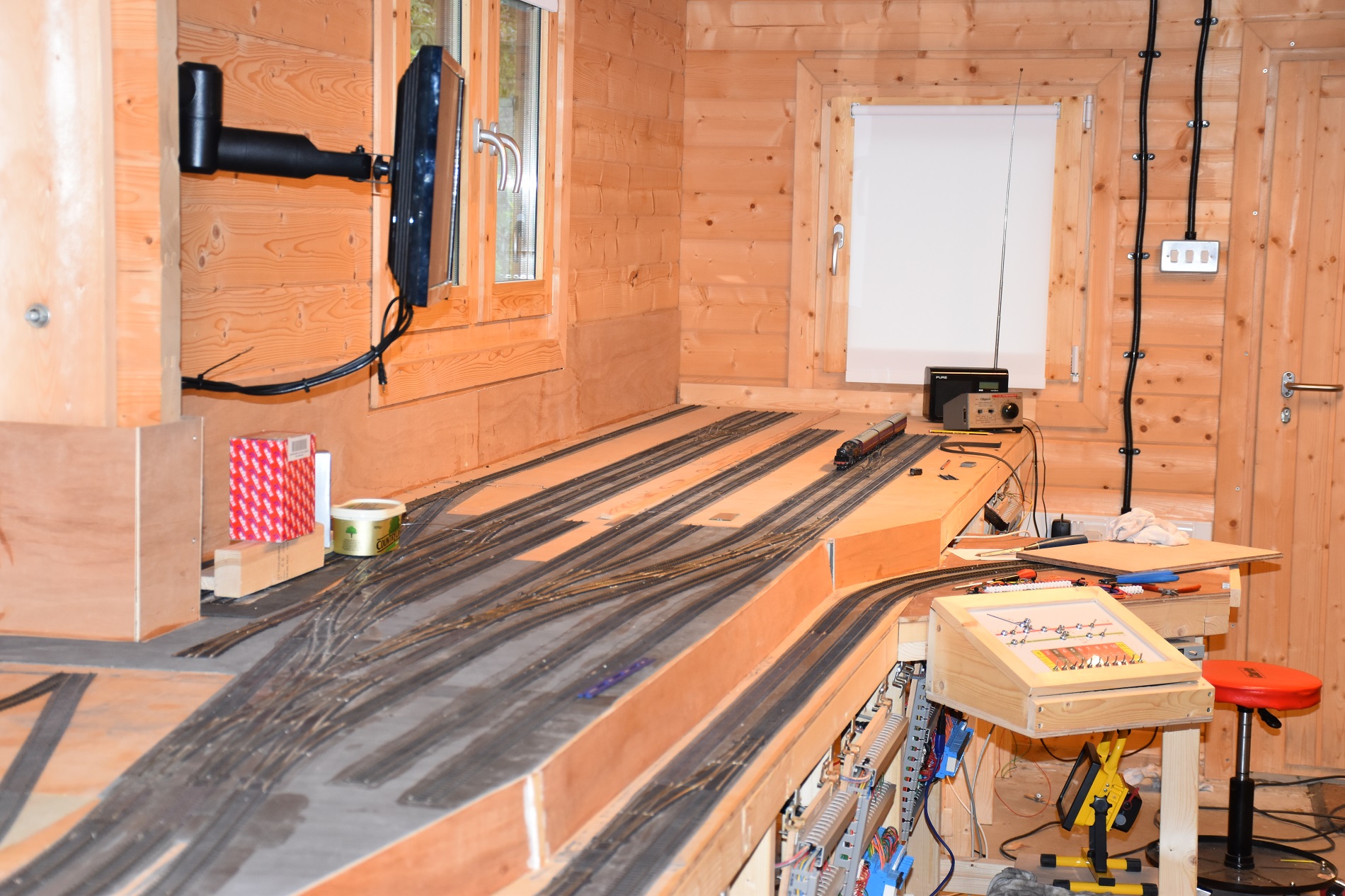
The integration of these technologies has made model railway automation accessible to a wider audience. Hobbyists no longer need to be experts in electronics or programming to create automated layouts. User-friendly devices like the PoKeys57U, combined with intuitive software, allow even beginners to design and implement complex automation systems. This democratization of technology has sparked a resurgence of interest in model railways, attracting a new generation of enthusiasts.
Model railway automation also serves as an excellent educational tool. By working on automated layouts, students and hobbyists can learn about concepts like control systems, programming, and mechanical engineering. These skills are not only valuable for the hobby itself but also provide a foundation for careers in engineering and technology.
Despite its many benefits, model railway automation does come with challenges. Designing and building an automated layout requires time, patience, and a certain level of technical knowledge. Additionally, the cost of components like CNC controllers and PoKeys57U devices can add up, especially for larger layouts. However, for many enthusiasts, the satisfaction of creating a fully automated model railway is well worth the effort.
In conclusion, model railway automation is a captivating example of how precision engineering and automation technologies can be applied on a smaller scale. By leveraging tools like CNC controllers and the PoKeys57U, hobbyists can create highly detailed and dynamic layouts that bring their miniature worlds to life. As we turn our attention to slip ring testing in the next chapter, we will see how the principles of precision and reliability that underpin model railway automation extend to other areas of engineering.
Slip Ring Testing – Ensuring Reliability in Rotating Systems
In the world of rotating machinery, slip rings play a critical role in transmitting power and electrical signals between stationary and rotating components. These devices are essential in applications ranging from wind turbines and industrial machinery to medical imaging equipment and even model railways. However, the reliability of slip rings is paramount, as any failure can lead to costly downtime or even safety hazards. This chapter explores the importance of slip ring testing, the methods used to ensure their performance, and how technologies like CNC controllers and the PoKeys57U contribute to this process.
Slip rings are electromechanical devices that allow the transfer of electrical signals and power across rotating interfaces. They are commonly used in systems where continuous rotation is required, such as in wind turbines, where they enable the transmission of power from the rotating blades to the stationary generator. Despite their simple appearance, slip rings are complex components that must withstand harsh conditions, including high speeds, temperature fluctuations, and mechanical stress.
To ensure the reliability of slip rings, rigorous testing is essential. Slip ring testing involves evaluating various parameters, such as electrical conductivity, signal integrity, and mechanical durability. One common test is the measurement of contact resistance, which assesses the quality of the electrical connection between the rotating and stationary parts. Excessive resistance can lead to power loss, overheating, and eventual failure. Another critical test is the evaluation of signal transmission, particularly in applications where slip rings are used to transmit data, such as in medical imaging equipment.
Advanced testing methods often involve the use of CNC controllers to simulate real-world operating conditions. For example, a CNC controller can be programmed to rotate a slip ring at varying speeds while monitoring its performance. This allows engineers to identify potential issues, such as wear and tear or signal degradation, under controlled conditions. The precision and repeatability of CNC controllers make them invaluable tools in slip ring testing, ensuring that each test is conducted with the same level of accuracy.
The PoKeys57U also plays a role in slip ring testing by providing a versatile platform for data acquisition and control. By connecting sensors and measurement devices to the PoKeys57U, engineers can monitor multiple parameters simultaneously, such as temperature, vibration, and electrical signals. This real-time data collection enables a comprehensive assessment of slip ring performance and helps identify potential failure points before they become critical.
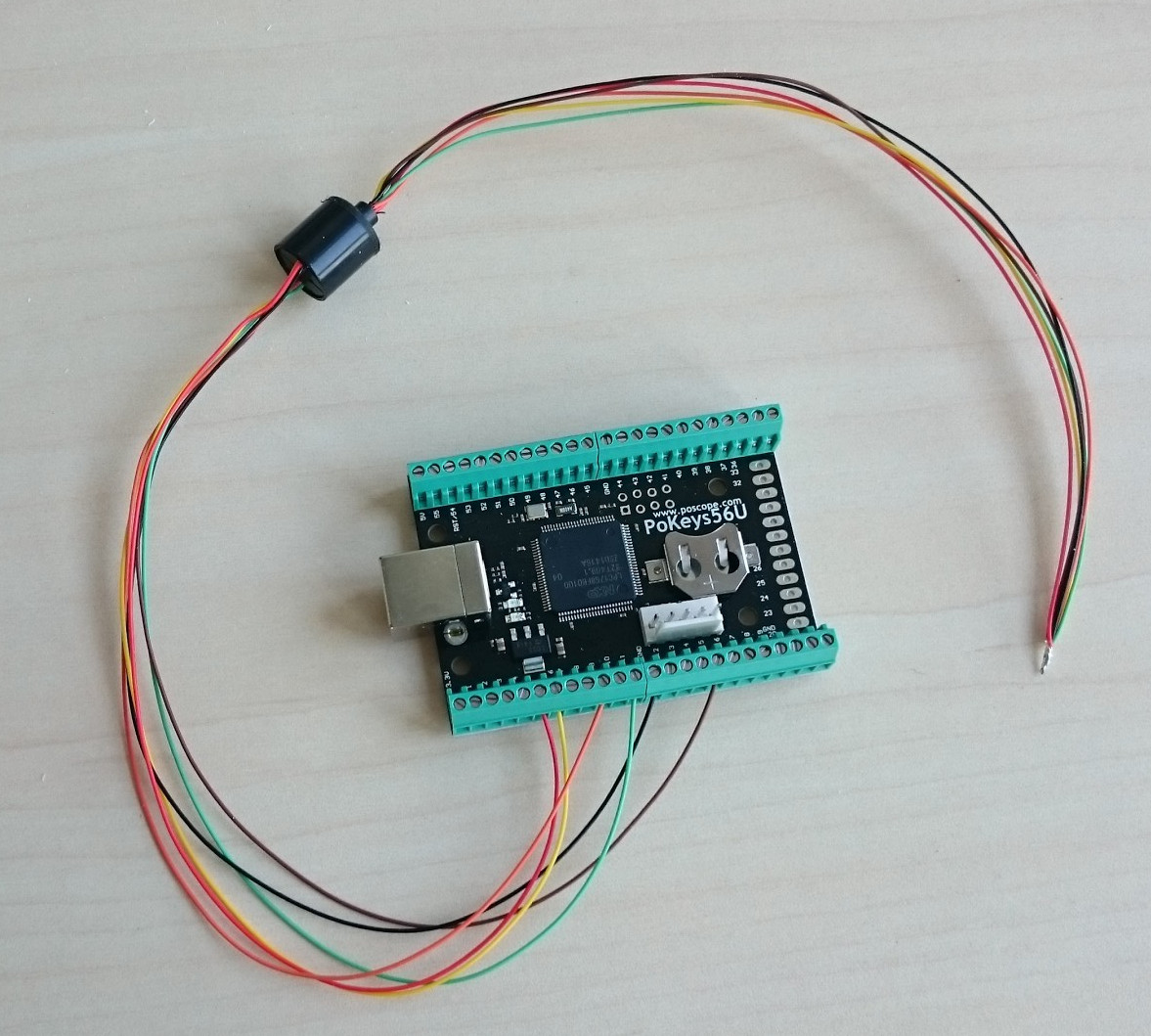
In addition to laboratory testing, slip rings are often subjected to field testing to evaluate their performance in real-world conditions. For instance, in wind turbines, slip rings must operate reliably for years under extreme weather conditions. Field testing involves monitoring the slip rings over an extended period, often using remote sensors and data loggers connected to devices like the PoKeys57U. This data is then analyzed to assess the long-term durability and reliability of the slip rings.
The importance of slip ring testing extends beyond industrial applications. In model railway automation, for example, slip rings are used to transmit power and signals to rotating turntables or animated scenery elements. Ensuring the reliability of these components is crucial to maintaining the functionality and realism of the layout. By applying the same testing principles used in industrial settings, hobbyists can ensure that their model railway systems operate smoothly and reliably.
Despite the advancements in testing technology, slip ring testing remains a challenging task. The complexity of slip rings, combined with the wide range of operating conditions they must endure, requires a thorough and systematic approach. However, with the aid of tools like CNC controllers and the PoKeys57U, engineers and hobbyists alike can achieve a higher level of confidence in the performance and reliability of slip rings.
In conclusion, slip ring testing is a vital process that ensures the reliability and longevity of rotating systems. By leveraging technologies like CNC controllers and the PoKeys57U, engineers can conduct comprehensive tests that simulate real-world conditions and identify potential issues before they become critical. As we reflect on the topics covered in this article—CNC controllers, PoKeys57U, model railway automation, and slip ring testing—we see a common thread of precision, reliability, and innovation that connects these diverse fields of engineering.
Unlocking the Secrets of Precision Plasma Cutting: A Guide to Torch Height Control
The Interconnected World of Precision Engineering and Automation
From the intricate movements of a CNC machine to the lifelike operation of a model railway, the technologies explored in this article—CNC controllers, PoKeys57U, model railway automation, and slip ring testing—demonstrate the remarkable advancements in precision engineering and automation. Each of these components plays a unique role in their respective domains, yet they are deeply interconnected by a shared commitment to accuracy, reliability, and innovation.
The CNC controller stands as the cornerstone of modern manufacturing, enabling the creation of complex components with micron-level precision. Its ability to coordinate multiple axes and adapt to various tasks has revolutionized industries ranging from aerospace to healthcare. Similarly, the PoKeys57U has emerged as a versatile enabler of automation, bridging the gap between sensors, actuators, and control systems. Its accessibility and flexibility have made it a valuable tool for hobbyists, educators, and engineers alike, fostering creativity and innovation in projects both large and small.
Model railway automation, while a niche application, serves as a testament to the broader potential of these technologies. By integrating CNC controllers and PoKeys57U devices, enthusiasts can create dynamic, lifelike layouts that replicate the complexity of real-world train systems. This microcosm of precision engineering not only brings joy to hobbyists but also serves as an educational platform for learning about control systems, programming, and mechanical design.
Finally, slip ring testing highlights the importance of reliability in rotating systems, ensuring that critical components can withstand the demands of real-world applications. The use of CNC controllers and PoKeys57U in this process underscores the interconnectedness of these technologies, as they work together to simulate operating conditions, monitor performance, and identify potential failures.
Together, these four topics paint a picture of a world where precision and automation are driving progress across industries. Whether it’s the production of a high-tech aerospace component, the operation of a model railway, or the reliability of a wind turbine, the principles of accuracy, control, and innovation remain constant. As technology continues to evolve, the integration of these tools will only deepen, opening up new possibilities for creativity, efficiency, and discovery.
In the end, the story of CNC controllers, PoKeys57U, model railway automation, and slip ring testing is one of collaboration and synergy. Each technology builds upon the others, creating a foundation for advancements that push the boundaries of what is possible. As we look to the future, it is clear that the principles of precision engineering and automation will continue to shape our world, driving progress and inspiring the next generation of innovators.